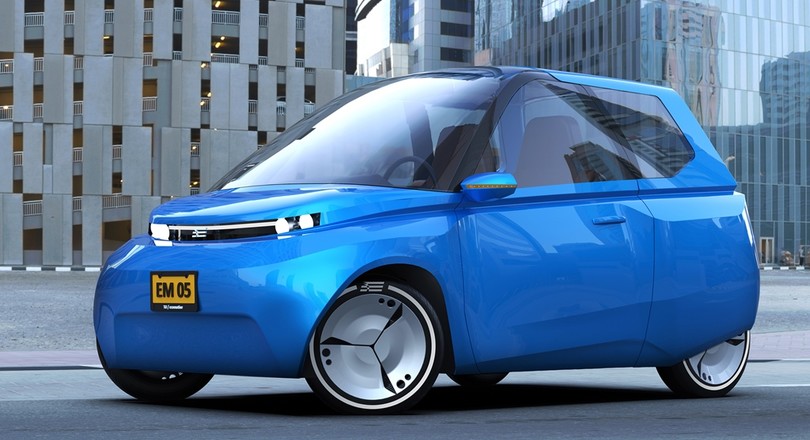
Cars are becoming more and more economical thanks to the use of light materials, but unfortunately producing materials such as aluminium and carbon consumes vast amounts of energy. The students in the TU/ecomotive team from Eindhoven University of Technology have addressed this problem with a car made of flax fibres and a bioplastic made of sugar, materials which can be made with about a sixth of the energy that other lightweight materials require.
The result is a cute little blue car, called the Noah, a modern city car which also offers snappy performance. With two electric motors, it is incredibly economical, achieving petrol-equivalent consumption figures of 300 km/l, about 850 (UK) MPG. This is mainly due to the car’s low weight – thanks to the special lightweight construction method, it weighs in at just 420 kg, including 60 kg of batteries. The chassis of this little car is made from sandwich panels (see photo below) – a construction method using light materials which still gives the vehicle the stiffness it needs.
Little energy
Even so, the students in the TU/ecomotive team wanted to take things a step further. They looked for materials that need as little energy as possible to make. 'Modern cars like the BMW i3 are made of light materials, which is great, because it reduces energy consumption on the road. The downside is that a lot of energy is needed to make the carbon and aluminium used,' explains Cas Verstappen, Automotive Technology student at Eindhoven University of Technology (not related to the Formula 1 racing driver). '185 GJ/tonne and 155 GJ/ton, respectively. That’s a lot compared with steel, which requires 30 GJ/tonne of energy to make. Our material requires 33 GJ/tonne.' The lightweight material used therefore only needs about the same energy to make as steel.

Bioplastic
Team TU/ecomotive opted for polylactic acid, a bioplastic made from sugar. The strong yet light end material was made by lining up a number of flax fibres and impregnating them with the bioplastic. This resulted in thin tapes, which were then placed on top of each other in 8 to 10 layers. 'In all different directions, because that’s the way to maximise strength.'
The result is a thin sheet of strong material that looks a bit like wood. You then take two panels, place a honeycomb structure between the two (a well-proven method to make something light and strong), and Bob’s your uncle: you now have a sandwich panel. The computer drawing below shows how versatile this material is – the entire Noah chassis is constructed from this type of sandwich panel.
Crash tests
OK, so the car is light, but how safe is it? 'It’s already safe enough to drive, but we’re going to apply to the RDW (the Dutch vehicle licensing agency) for a registration certificate, so we can try it out on the road. We can’t do crash tests, but we have to provide simulations that show how strong the car is,' says Verstappen.
A metal car has crumple zones that deform and absorb energy in the event of a severe collision, but this is not possible with sandwich panels. 'We have incorporated pyramid-shaped structures that function as crumple zones.'
Responsible
According to Verstappen, the materials chosen are very sustainable. Unlike with carbon, no fossil fuels are needed to make them. 'Flax even absorbs CO2 from the air while the plant is growing, and so does sugar,' says Verstappen. At the end of its life, the biocomposite can be crushed and used as a raw material for other products. Non-biological components, such as steel, can be recycled in existing processes.
Raising awareness

Noah can reach 110 km/h, and has a range of 240 km when fully charged. Nevertheless, the vehicle will not enter mass production. The TU/ecomotive team’s aim is to make car manufacturers more aware of the possibilities of lighter construction with more energy-efficient materials. 'The sector is very conservative, so we’re hoping that we can offer manufacturers some inspiration. We’ve already arranged a few appointments to visit car manufacturers.'
Verstappen thinks that change in the automotive industry will be slow. 'I hope that more natural materials will gradually appear in cars. Some companies are already moving in this direction, such as BMW which uses bamboo grass in the doors of its i3. It will always happen first with parts which don’t affect safety.'
The students in the TU/ecomotive team presented their Noah to participating companies and the press at sponsor Suikerunie on 5 July. The next day they demonstrated their car in Eindhoven.
If you found this article interesting, subscribe for free to our weekly newsletter!
Images: TU/ecomotive / Bart van Overbeeke
Nieuwsbrief
Vond je dit een interessant artikel, abonneer je dan gratis op onze wekelijkse nieuwsbrief.