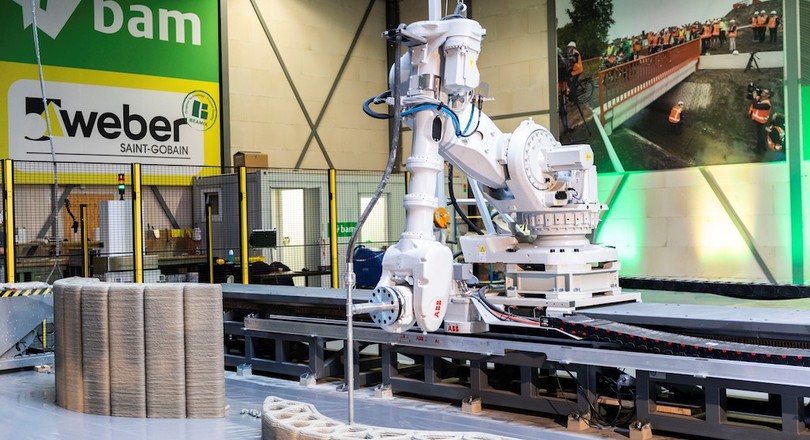
In Eindhoven, BAM Infra and Weber Beamix have started operating a 3D concrete printer. According to these companies, this is the first industrial production location for 3D concrete printing. The printer will be used to make parts for buildings and structures.
This system’s innovative character lies in its reinforcement, which provides extra strength in concrete structures, and is printed together with the concrete. This involves an ingenious method of placing the steel reinforcement rods alongside the nozzle that deposits the concrete.
Curved shapes and less material
According to the initiators, there is demand for an industrial production location where customers can order custom concrete structures. The advantage of 3D concrete printing is that it allows curved, organic shapes to be made, which are difficult to manufacture using conventional formwork. Formwork is rendered unnecessary, with the added benefit of less waste.
Printing concrete also allows sufficiently resilient structures to be made with less material. The net result is lower CO2 emissions, as large volumes of this greenhouse gas are released during the production of cement, one of the main components of concrete. The less concrete, the lower the emissions. A good example is the bicycle bridge that was printed at Eindhoven University of Technology in 2017.
Concrete printing becoming more popular
There are a number of completed and ongoing projects that use a concrete printer. A good example is De Vergaderfabriek in Teuge, in the province of Gelderland, where building work is about to start. Another is the house made of organic forms entirely produced by 3D printing, which was presented at the Salone del Mobile in Milan in April 2018.
The company CyBe, also Dutch, is involved in both projects. It has already been working on printing buildings and concrete structures on-site for years. CyBe was also involved in setting up the concrete printing research at Eindhoven University of Technology.
Hoe does it work?
The process starts with a stock of dry mortar in a silo. When the machine is switched on, the dry material runs out of the silo. Water is added, after which a pump sends the liquid mortar through a hose to a nozzle that is attached to a robot arm. This accurately follows software instructions. All the coordinates of this arm are calculated according to the 3D drawing of the structure being made.
The main idea behind concrete printing is to create a 3D shape by adding layer after layer of liquid concrete. These layers are still wet when they first come into contact with each other, so they adhere to each other when the concrete hardens, giving the printed structure its strength.
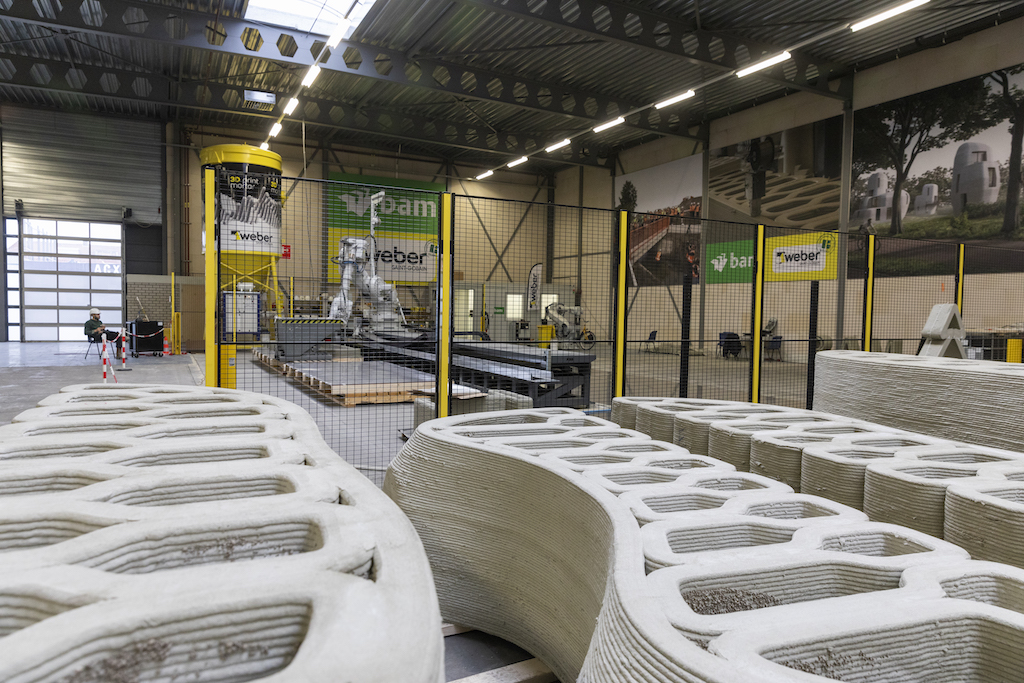
Research
BAM and Weber are not limiting their activities to printing concrete structures at the new production location. They are also carrying out research into the best concrete mixes for printing, and the ideal printer settings. There are lots of parameters which can be set, such as the speed of the print head, the size of the nozzle, the thickness of each layer, and so on.
For example, the margin between the concrete mixture being too wet and too dry is very narrow. When it is wet, in other words just after a layer has been printed, it must be resilient enough to be able to bear multiple layers above it. If the concrete is too liquid, it collapses under the weight of the following layers. On the other hand, it must be moist enough for the layers to adhere to each other well, so the building does not fall apart after drying.
BAM and Weber Beamix are not the only project partners. Eindhoven University of Technology, which conducts a lot of research in this area, and the companies Bekaert, Witteveen+Bos and Van Wijnen are also involved.
Images: BAM Infra
If you found this article interesting, subscribe for free to our weekly newsletter!
Nieuwsbrief
Vond je dit een interessant artikel, abonneer je dan gratis op onze wekelijkse nieuwsbrief.