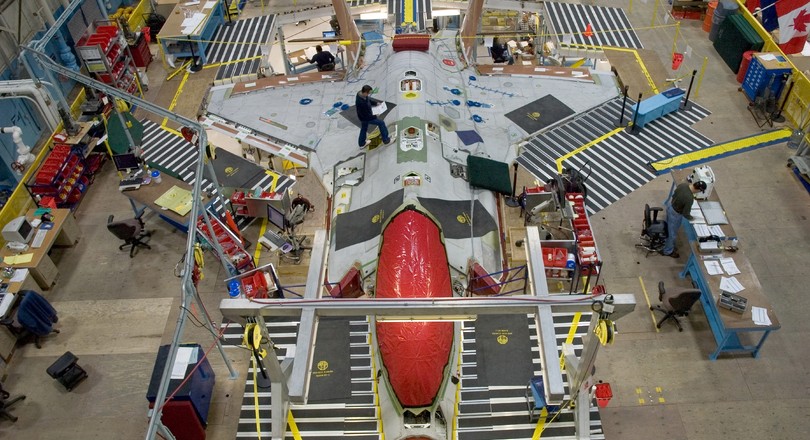
De F-35 Lightning II, voorheen bekend onder de naam Joint Strike Fighter (JSF), moet nog dit jaar voor het eerst het luchtruim kiezen. Met een verwacht orderaantal van 5500 is de straaljager een echt massaproduct. Vliegtuigbouwer Lockheed Martin haalt alles uit de kast om de grootschalige fabricage te stroomlijnen en een hoog productietempo te garanderen. ‘Een toestel per dag is zonder twijfel haalbaar.’
Dit artikel verscheen eerder in De Ingenieur 2006-18. Auteur: Thijs van Velzen
Warme lucht stroomt de auto in wanneer de chauffeur zijn portier opent voor een inspectie van de banden. De zon staat nog niet op zijn hoogste punt, maar het kwik is reeds boven de 40 ˚C gestegen. De autobanden moeten schoon zijn voor het rijden op het platform, legt hij uit. Rotzooi kan in een van de vliegtuigen of straalmotoren terechtkomen en voor schade zorgen. Het asfalt is dan ook keurig schoon. Nergens is een vuiltje of kiezeltje te bekennen. Het militaire bewakingpersoneel op Naval Air Station Fort Worth Joint Reserve Base in de Amerikaanse staat Texas ziet streng toe op naleving van de regels. Met de maximaal toegestane snelheid van tien mijl per uur kruipt de auto over het zwarte asfalt, terwijl aan de linkerkant van het platform hangar na hangar voorbijglijdt.
In de eerste dertien loodsen staan F-16’s. De meeste zijn gloednieuw, anderen krijgen een onderhouds- of opknapbeurt. Op de militaire basis is namelijk niet alleen de luchtmacht gevestigd. Lockheed Martin produceert in Air Force Plant 4, dat onderdeel is van de basis, al jaren F-16’s. In april leverde de fabrikant het 4300e toestel en er staan nog tal van orders in de boeken. Toch heeft de straaljager zijn langste tijd gehad. De laatste hangar van het rijtje huisvest het eerste exemplaar van de gedoodverfde opvolger: de F-35 Lightning II. Het toestel, dat voorheen onder de naam Joint Strike Fighter (JSF) door het leven ging, is begin juli met veel fanfare gepresenteerd.
In de loods is daar weinig meer van te merken. Het zijn lange dagen voor productietechnicus Kevin McGagin en zijn team. McGagin is verantwoordelijk voor de laatste werkzaamheden aan de AA-1, het eerste exemplaar van de F-35 dat nog dit jaar zijn luchtdoop moet krijgen. ‘Het zijn de laatste loodjes’, vertelt hij tijdens zijn lunchpauze. ‘Bij de grondproeven eerder dit jaar was het toestel voorzien van een aantal niet-gecertificeerde onderdelen die we nu vervangen. Daarna is het toestel gereed voor de eerste testvlucht. Alles past perfect, het is een soort bouwpakket. De hele productie en assemblage van de AA-1 is nagenoeg probleemloos verlopen, wat niet eerder vertoond is bij de vervaardiging van het eerste exemplaar van een gevechtsvliegtuig. Bijna alles liep op rolletjes.’
MASSAPRODUCT
Het is allerminst een toevalstreffer dat de productie van het eerste exemplaar in vergelijking met voorgaande toestellen zo gesmeerd is verlopen. Lockheed Martin spaart met het oog op de enorme productieaantallen kosten noch moeite om de fabricage van de F-35 zo eenvoudig en efficiënt mogelijk te laten verlopen. De landen die aan het programma deelnemen, willen in eerste instantie 3153 kisten aanschaffen. Met de verkoop aan andere landen en vervolgorders kan dit aantal oplopen tot 5500, zo becijfert de vliegtuigbouwer. De F-35 is een waar massaproduct. De fabricage daarvan veronderstelt een andere benadering van de productie dan in de militaire vliegtuigbouw gebruikelijk is. Niet langer staat alleen de kwaliteit van het eindproduct centraal, zoals veelal in de defensiesector het geval is, ook het fabricageproces zelf speelt een belangrijke rol.
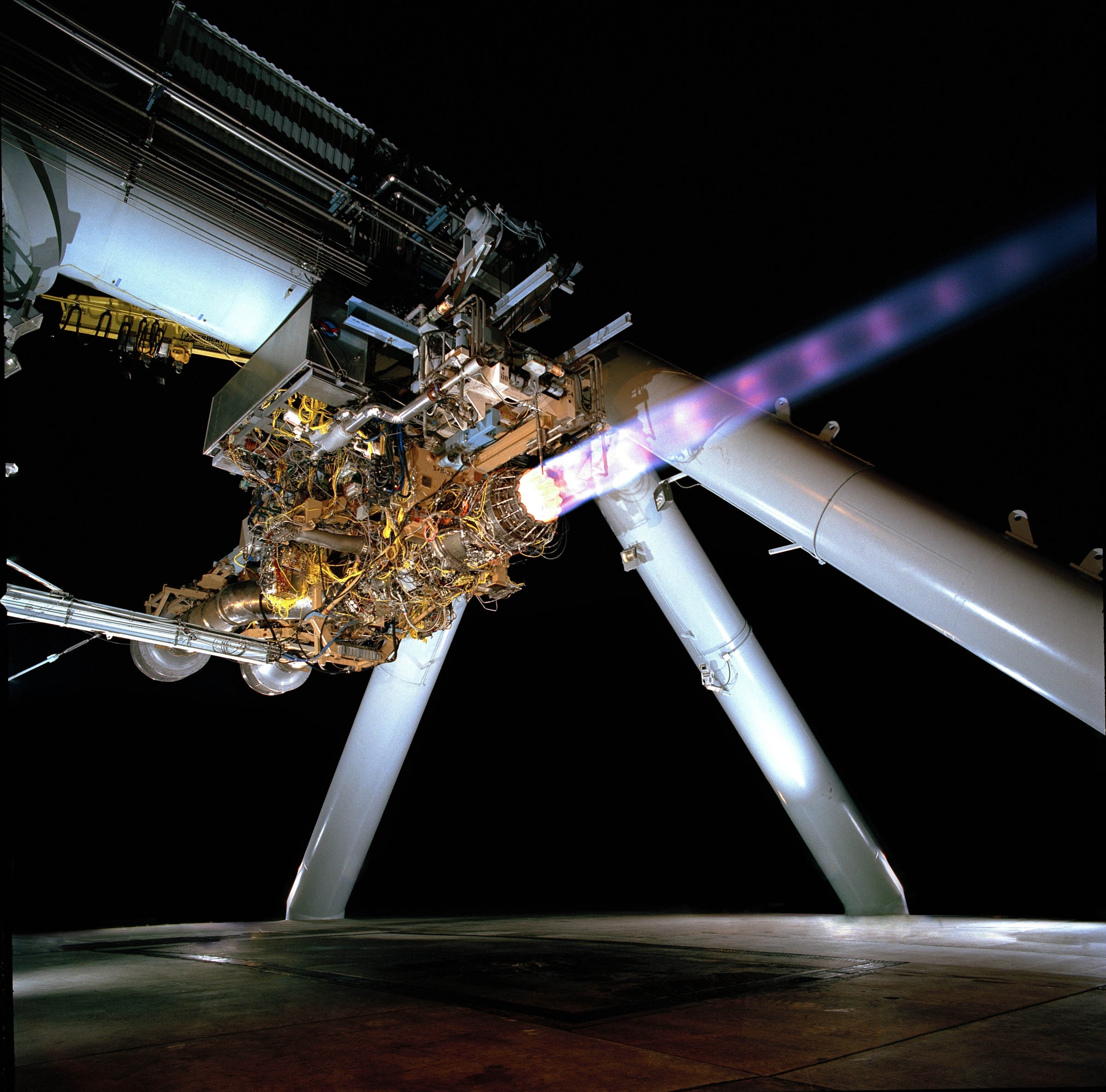
Om de voordelen van schaalgrootte te benutten heeft Lockheed Martin bijna alle traditionele opvattingen over vliegtuigbouw overboord moeten zetten. De inspanningen van de Amerikaanse fabrikant richten zich met name op het omlaag brengen van de arbeidskosten. Arbeid vormt namelijk een van de grootste kostenposten binnen het project. Om dat te bereiken streeft de vliegtuigbouwer allereerst naar een reductie van het aantal onderdelen in het vliegtuig zelf, wat de arbeidsintensieve assemblage vereenvoudigt. Daarnaast moeten slimme logistiek, speciaal gereedschap en automatisering het werk makkelijker maken en arbeidskrachten sparen.
VARIANTEN
De F-35 komt in drie varianten op de markt, omdat de straaljager niet alleen als vervanger van de F-16 geldt. Het toestel volgt ook de gevechtsvliegtuigen F/A-18 Hornet, AV-8B Harrier en A-10 Thunderbolt op. ‘Hierdoor neemt het potentiële productieaantal uiteraard toe, wat het programma ten goede komt’, vertelt James Latham, directeur internationale betrekkingen van het F-35-programma. ‘Maar omdat deze vliegtuigen verschillende eigenschappen en functies hebben, is het noodzakelijk een aantal varianten van de Lightning II te maken. Deze uitvoeringen onderscheiden zich voornamelijk wat betreft het opstijgen en landen.’
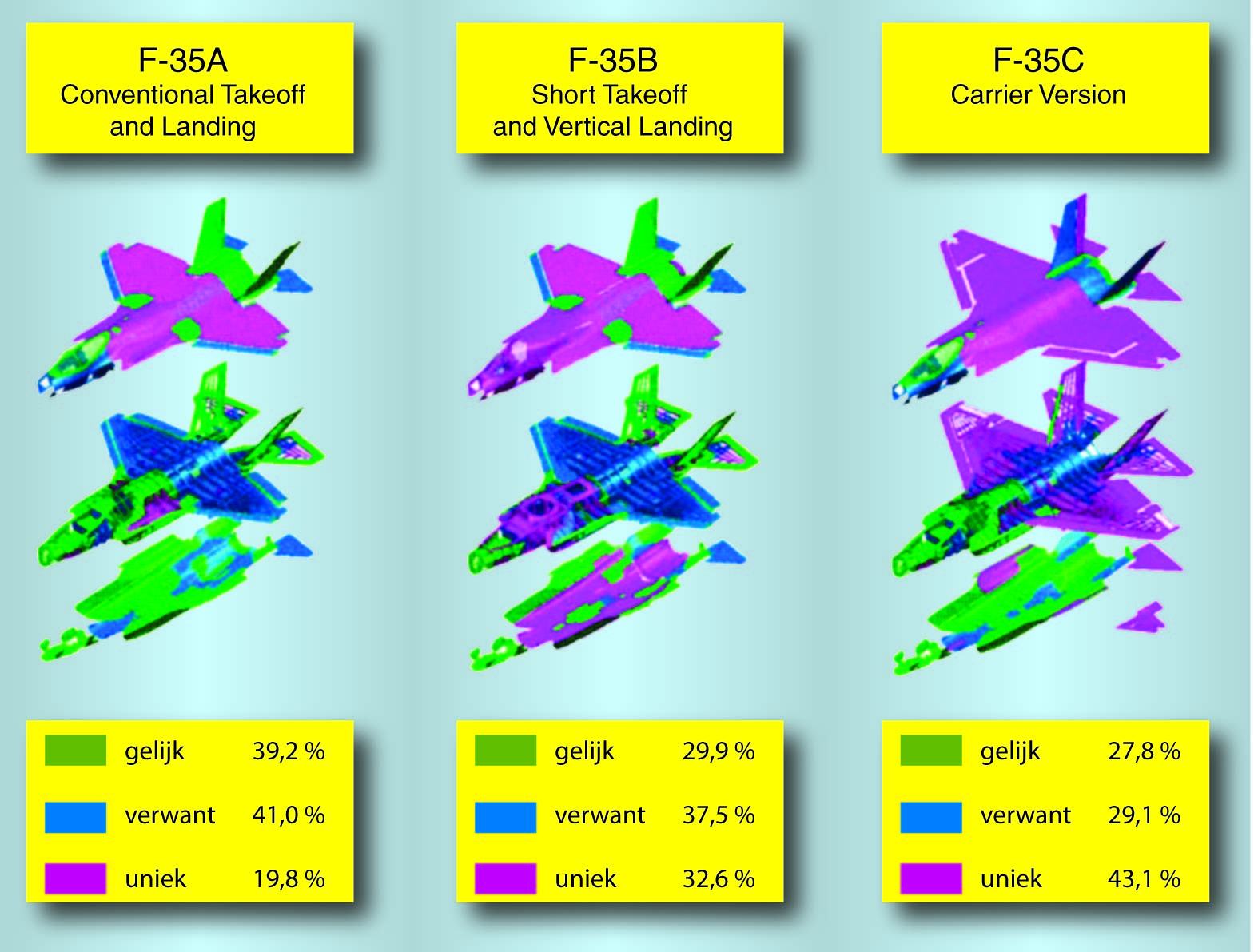
Variant A van de F-35 staat ook wel bekend als Conventional Takeoff and Landing (CTOF). Dit toestel geldt als opvolger van de F-16 en heeft vergelijkbare start- en landeigenschappen. De F-35B Stovl, wat staat voor Short Takeoff Vertical Landing, heeft een relatief korte startbaan nodig en kan verticaal landen. Het derde type, de F-35C Carrier Version (CV), is voorzien van een vanghaak voor het landen op een vliegdekschip. ‘Ook zijn bepaalde onderdelen van de F-35C CV zwaarder uitgevoerd, omdat het starten met een katapult een grote belasting veroorzaakt’, voegt Latham toe.
De verschillende eisen voor de start en de landing compliceren het ontwerptraject, vervolgt hij. ‘Daar komt bij dat de Lightning II zowel andere vliegtuigen als gronddoelen moet kunnen aanvallen. Deze combinatie van taken brengt eveneens een heel pakket aan eisen met zich mee. Binnen het F-35-programma zorgt de nadruk op de massafabricage nog voor verdere complexiteit. Zeker wanneer de drie varianten met dezelfde productielijn moeten worden gebouwd.’
George Law, de hoofdingenieur van de F-35, weet als geen ander hoe complex het ontwerpproces was. ‘En nog steeds is’, corrigeert hij. ‘Het ontwerp is eigenlijk nooit af, maar wordt gedurende de looptijd van het programma steeds verbeterd.’ Law is vanaf het prille begin bij het programma betrokken en werkte in de jaren negentig aan de ontwikkeling van de drie demonstratiemodellen, die destijds onder de naam X-35 door het leven gingen. Voor zijn bijdrage aan het project ontving hij in 2002 de Aircraft Design Award van het American Institute of Aeronautics and Astronautics (AIAA).
‘Voorafgaand aan het daadwerkelijke ontwerpproces is voor elke variant in een configuratietekening de uitwendige geometrie weergeven’, legt hij uit. ‘Ook is voor de Stovl-variant een grof ontwerp gemaakt van de interne structuur en de plaatsing van subsystemen. Vervolgens is bekeken of en hoe dat ontwerp te vertalen is naar de andere twee varianten. Uiteraard volgen uit deze vertaalslag nieuwe inzichten, waardoor het originele ontwerp weer verandert. Het is zodoende een sterk iteratief proces. Na dit proces is een detailontwerp voor de Stovl-variant uitgewerkt, dat wederom de basis vormde voor de andere twee uitvoeringen.’
DETAILONTWERPEN
Het productieproces als complicerende factor komt pas echt in beeld bij het maken van de detailontwerpen, weet Law. ‘Bij het uitwerken van de detailontwerpen heeft steeds een vraag centraal gestaan: moet het anders en zo ja waarom? We streven immers naar de ontwikkeling van drie varianten die zoveel mogelijk op elkaar lijken. Als de verschillen groot zijn, komen er eigenlijk drie compleet nieuwe toestellen tot stand.’ De implicaties spreken voor zich. Sterk van elkaar verschillende straaljagers zijn niet met dezelfde productielijn en hetzelfde gereedschap te maken.
‘Een enorme winst is te behalen op de luchtvaartelektronica en de straalmotor die binnen een gevechtsvliegtuig een grote kostenpost voor rekening nemen’, stelt Law. De drie varianten maken dan ook gebruik van dezelfde avionica en motor. Er zijn overigens wel twee typen motoren voor de F-35 ontwikkeld. Pratt & Whitney levert de F135 en General Electric bouwt samen met Rolls-Royce de F136. ‘Voor het toestel maakt het echter niet uit welke motor wordt ingebouwd’, geeft de hoofdingenieur aan. ‘De aansluitingen zijn exact hetzelfde en ook de aansturing is identiek. Het gereedschap voor de montage van de motoren is eveneens helemaal gelijk.’
Bij de start van het programma ging het ontwerpteam uit van meer identieke onderdelen in de drie varianten dan uiteindelijk het geval is. Law: ‘Bezien vanuit de prestaties van de vliegtuigen bleek een groter percentage afwijkende componenten noodzakelijk. Veelal is het verschil beperkt: een onderdeel is bijvoorbeeld iets dikker of langer. Dit zorgt weliswaar voor een stijging van de kosten, maar die toename is beperkt. Voor het productieproces maakt een kleine variatie niet heel veel uit. Het onderdeel is dan nog te vervaardigen met dezelfde machines en gereedschappen.’
Grotere motor
Het streven naar veel identieke componenten resulteert in sommige gevallen echter in een suboptimale oplossing. De ontwikkeling van drie varianten in combinatie met veel nadruk op de fabricage leidt tot consensus in het ontwerp. Een voorbeeld is de Integrated Power Package (IPP), een kleine gasturbine die zich aan de achterzijde onder de straalmotor bevindt.
De IPP heeft als taak de motor te starten. Ook genereert het apparaat elektriciteit. Vanwege de complexiteit en de compactheid van het ontwerp is het een relatief kostbaar systeem. Afgelopen zomer bleek dat de F-35C Carrier Version meer vermogen nodig heeft, wat een vergroting van de IPP vereist. Toen is besloten de grotere gasturbine ook voor de twee andere varianten te gebruiken. Deze toestellen vliegen straks dus met een iets zwaarder systeem dan strikt noodzakelijk is. De productie van verschillende IPP’s zou echter veel kostbaarder zijn.
SAMENVOEGEN
Drie modellen met veel identieke componenten vormen echter nog geen garantie voor eenvoudige fabricage en assemblage. Met name in het ineenzetten gaan veel manuren zitten met evenredig hoge kosten. De oplossing van Lockheed Martin is even eenvoudig als effectief: verklein het aantal onderdelen. Dat betekent concreet dat verschillende componenten worden samengevoegd tot een onderdeel. ‘Het samenvoegen tot een grotere component gaat doorgaans gepaard met een toename van de productiekosten per onderdeel’, vertelt hoofdingenieur George Law. ‘Deze kostenstijging hangt onder meer samen met de grote en kostbare machines die voor de vervaardiging noodzakelijk zijn en met een groter materiaalverlies. Toch weegt de stijging op tegen de reductie van de arbeidskosten.’
Bij de verkleining van het aantal onderdelen speelt de opkomst van composietmaterialen een belangrijke rol. De verwerking van composieten is nog steeds relatief duur, maar door de ontwikkeling van nieuwe technieken dalen de kosten de laatste jaren sterk. Met name voor grote componenten met een complexe vorm gelden vezelversterkte kunststoffen als een aantrekkelijk alternatief. Het hele toestel bestaat voor zo’n 40 % uit composieten.
Het resultaat mag er zijn. In vergelijking met de F-22 Raptor, de superieure onderscheppingsjager die eveneens door Lockheed Martin wordt gebouwd en alleen bestemd is voor de Amerikaanse luchtmacht, is het aantal onderdelen in de F-35 zeventien maal kleiner. De assemblage moet zodoende veel minder manuren kosten en de doorlooptijd zal aanzienlijk korter zijn. ‘Het toestel is ontworpen voor productie’, aldus Law.
SIMULATIE
‘Elke dag moet een toestel van de lijn rollen’, zegt Edward Linhart, vicepresident productie bij Lockheed Martin, terwijl hij door de reusachtige hal direct naast de kantoren van de vliegtuigfabrikant loopt. De hal, waar de eindassemblage van de F-35 plaatsvindt, is duidelijk zijn werkterrein. In het 1617 m lange gebouw werken honderden mensen aan het ineenzetten van F-16’s en secties van de F-22 Raptor. De witte vloer is brandschoon. Abrupt stopt Linhart als hij ergens een slijtplek in de verflaag ziet. ‘Die vloer is hier toch net opnieuw geverfd?’, vraagt hij aan een werknemer, die bevestigend antwoordt. ‘Vreemd. Ik denk dat ze gewoon te hard werken.’
Er wordt inderdaad hard gewerkt, want de hal ondergaat een grootschalige transformatie. ‘Dit was het kloppende hart van de F-16-productie’, vertelt Linhart. ‘Tijdens het piekjaar 1987 zijn hier 284 toestellen gemaakt.’ De F-16’s zijn nu naar het achterste deel van de ruimte verplaatst om ruimte te maken voor hun opvolger.
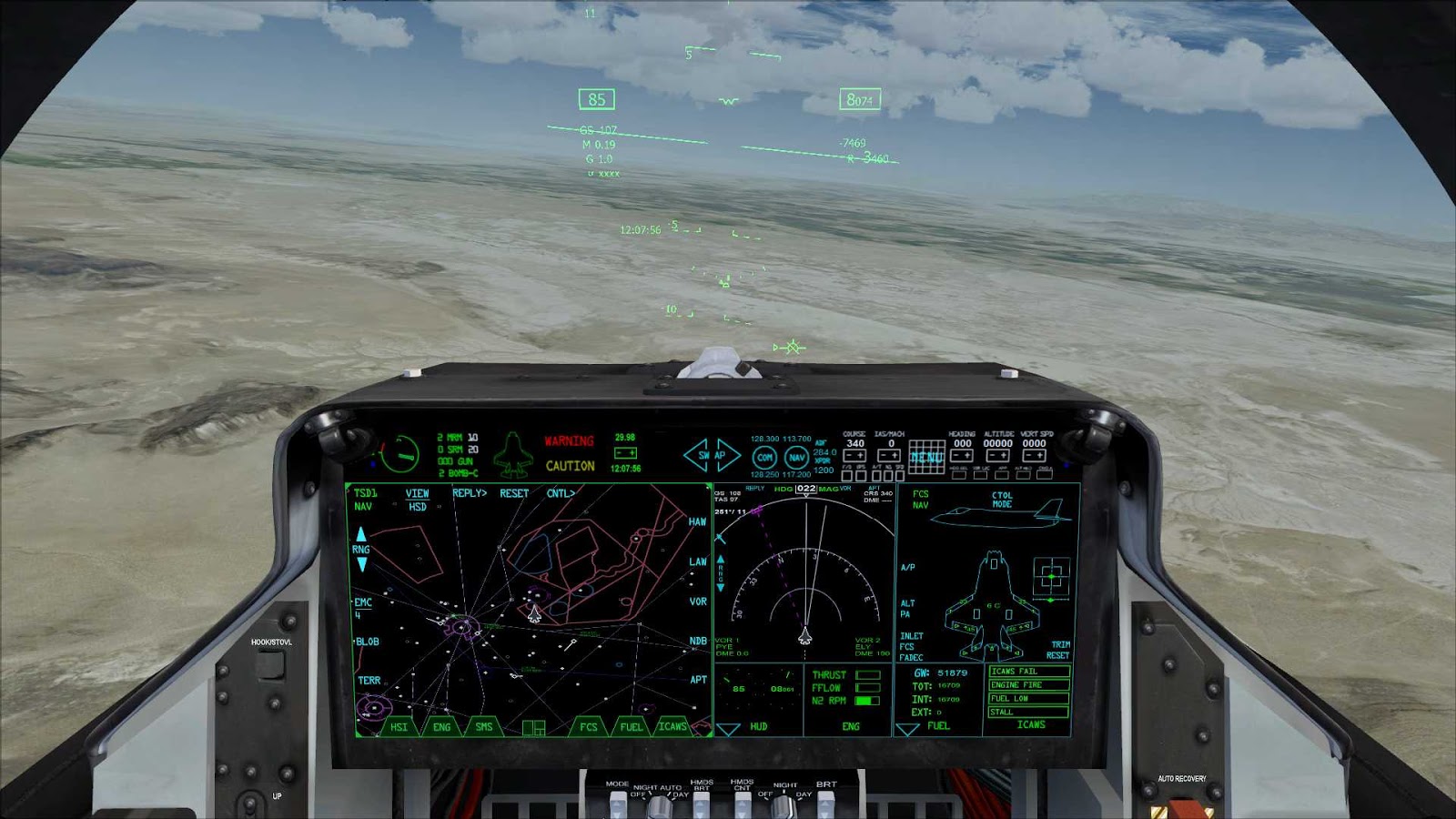
De hal is nog lang niet gereed voor massafabricage van de F-35, maar Linhart twijfelt niet aan de haalbaarheid van het hoge productietempo. ‘Met behulp van speciale computerprogramma’s is het hele proces tot in detail in kaart gebracht. Deze programma’s maken simulatie van de hele assemblage mogelijk, zodat alle mogelijke knelpunten al bekend zijn voordat de grootschalige productie start. Ook is het mogelijk om het ineenzetten van een specifiek toestel te simuleren. Bij het maken van de F-35 AA-1 is dit gedaan. Voordat alle onderdelen hier in Fort Worth waren, leverden de projectpartners informatie over de dimensies van de componeten aan. Met een simulatie op basis van deze gegevens is gekeken of alles ook daadwerkelijk paste.’
FREESBANK
De eerste machines en installaties zijn reeds in gebruik. Meest in het oog springend is een omvangrijke vijfassige freesbank die in een afgeschermde ruimte staat en onderdelen tot ongeveer 15 m kan bewerken. ‘De freesbank is onder meer bestemd voor bewerking van de kunststofvleugelhuiden’, vertelt Linhart. ‘Omdat de Lightning II onzichtbaar moet zijn op de radar, zijn de toleranties zeer klein. Een minimale afwijking in de geometrie kan grote gevolgen hebben voor deze stealth-eigenschappen.'
'De freesbank werkt met een gegarandeerde tolerantie van 0,2 mm, maar presteert in praktijk beter. Bij de 10,7 m lange bovenste vleugelhuid voor de F-35 AA-1 bedroeg de afwijking slechts 0,05 mm. Om een dergelijke nauwkeurigheid te halen staat de hele installatie in een geconditioneerde ruimte, waar het constant 22,8 ˚C is.’
Voor de inspectie van de vleugelhuiden maakt Lockheed Martin gebruik van een nieuwe techniek uit eigen stal. De Laser Ultrasonic Test (LaserUT) is in staat een zeer snelle en nauwkeurige controle op onregelmatigeheden uit te voeren. Hiertoe maakt het apparaat gebruik van twee lasers. De eerste pulserende laser zorgt voor een lokale temperatuurstijging van het oppervlak, die hoogfrequente schokgolven in het materiaal veroorzaakt. Een zwakke plek of een insluiting in het materiaal zorgt voor een verstoring van de golven, wat de tweede laser detecteert.
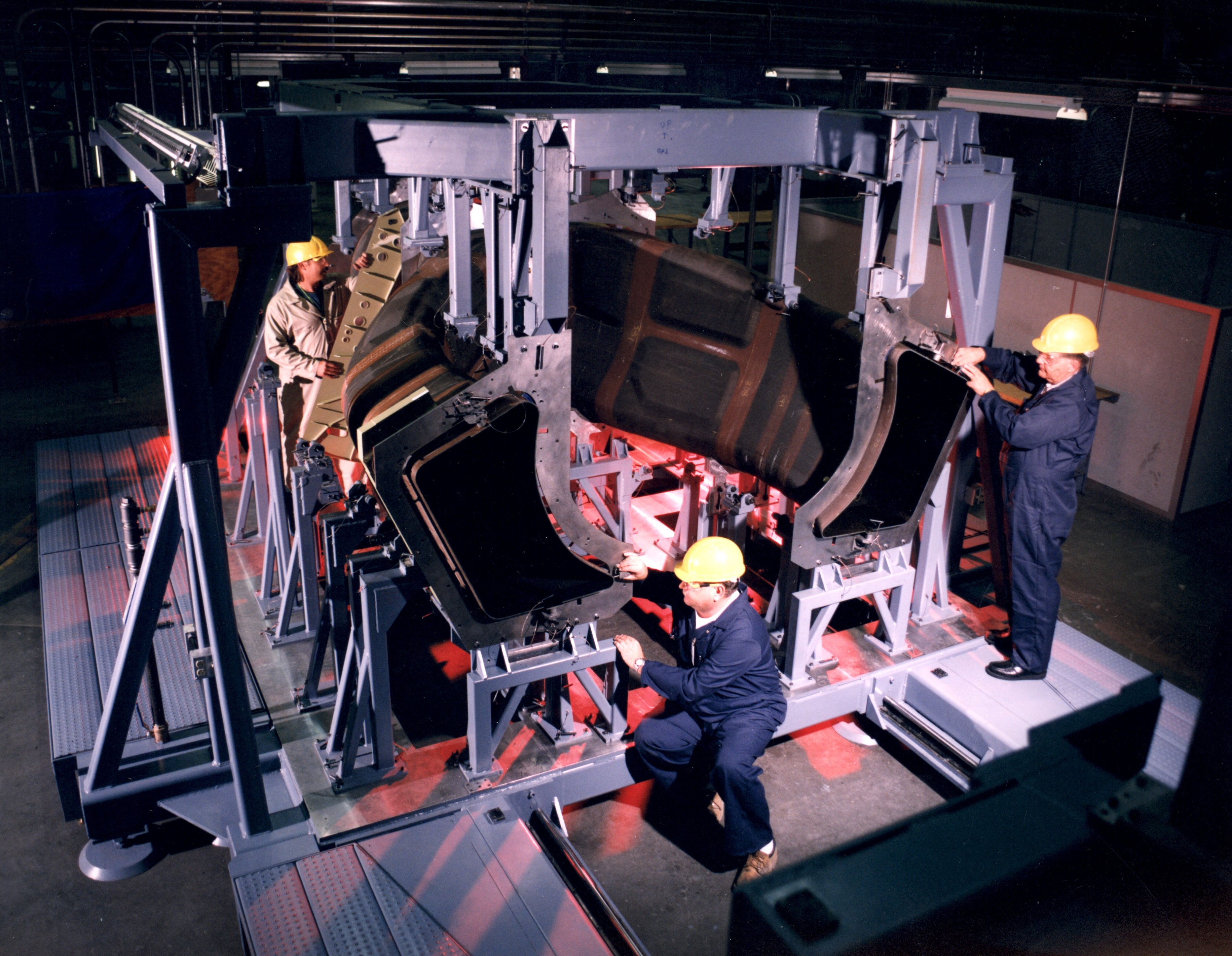
‘De testmethode is veel nauwkeuriger dan voorgaande technieken waarbij een onderdeel in zijn geheel in een vloeistof werd gedompeld’, zegt Linhart, die over de exacte werking van de LaserUT niets kwijt wil. ‘Daarnaast neemt de nieuwe methode tien maal minder tijd in beslag en bedragen de arbeidskosten slechts 10 %.’
De zogenoemde autodrill levert een vergelijkbare bijdrage. De ruim 5 m hoge installatie boort gelijktijdig gaten in de vleugelhuid en -constructie. Ook brengt de machine een verbinding tussen de verschillende delen tot stand. Bij de productie van de F-35 AA-1 maakte de automatische boor zo’n 6700 gaten binnen 24 uur. Slechts één gat voldeed niet aan de vereiste tolerantie van 50 µm. De oorzaak bleek een fout in de digitale invoer. Het hele proces verloopt bijna volledig zonder tussenkomst van mensen.
Hetzelfde geldt voor de spuithal, waar de vliegtuigen in de gewenste kleur worden gespoten en tevens een speciale stealth-coating krijgen. Het opbrengen van de coating luistert zeer nauw, omdat een te dikke of te dunne laag invloed heeft op het radarprofiel. Zelfs voor ervaren spuiters is het een tijdrovend en kostbaar proces. Voor het aanbrengen van deze secret sauce, de mysterieuze coating die radarsignalen absorbeert, zet de vliegtuigbouwer een achtassige robotarm in. De arm kan elke hoek bereiken en elke kromming volgen. Tussenkomst van ervaren spuiters behoort in principe tot het verleden.
VERHOOGDE VLOER
Het eerste assemblagestation waar de verschillende onderdelen aan elkaar worden gekoppeld, is ook al gereed. Het station bestaat uit een verhoogde vloer met uitsparingen in de vorm van de straaljager. Door de verhoging kunnen meer mensen gelijktijdig aan het toestel.werken. ‘Een kraan hijst eerst de centersectie in het station’, legt Linhart uit. ‘Hierna volgt het voorste deel van de romp, de vleugel en tot slot de achterste rompsectie. Het assemblagesysteem dat de verschillende delen uiteindelijk bij elkaar brengt, zorgt ook voor de uitlijning en maakt tussenkomst van mensen grotendeels overbodig.'
'Lasers registreren de exacte positie van de delen zeer nauwkeurig, waarna het systeem aangeeft of de uitlijning van de delen juist is. Dat is wederom met het oog op de stealth-eigenschappen cruciaal. Tijdens de assemblage van de F-35 AA-1 gaf het systeem aan dat de achterste rompsectie 0,3 mm te ver naar rechts stond. De actuatoren kregen vervolgens de opdracht om die 0,3 mm op te schuiven. Niemand heeft deze verschuiving gezien, maar de volgende meting met de lasers bevestigde een volledige juiste uitlijning. Een dergelijk accuraat assemblagesysteem is niet eerder gebruikt.’
Laatste deel van de lijn
Het laatste deel van de productielijn bestaat alleen nog op papier. Linhart wijst naar vijf F-16’s die even verderop in de hal staan. ‘Daar komt de bewegende productielijn, waar de laatste werkzaamheden aan de F-35 moeten plaatsvinden. Vanuit de assemblagestations zet een kraan de toestellen op de lijn. Elk vliegtuig passeert vervolgens een aantal stations, die zich met het toestel over een bepaalde afstand door de hal verplaatsten. Daarna keren ze terug naar hun beginpositie om de volgende kist onder handen te nemen.’
Sinds de Tweede Wereldoorlog, toen in dezelfde hal B-24-bommenwerpers aan de lopende band in elkaar werden gezet, is deze techniek niet meer ingezet bij de productie van militaire vliegtuigen. Voor het ontwerp van de bewegende lijn nam Lockheed Martin technici van autofabrikant Toyota in de arm. Eerder assisteerden zij Boeing bij het opzetten van een productielijn voor de fabricage van het verkeersvliegtuig 737.
‘De lijn moet het hele productieproces verder versnellen. Tijdens de eerste fase van de fabricage verplaatst een vliegtuig 25 mm per uur, maar in 2012 bedraagt de snelheid 1,2 m per uur’, geeft Linhart aan. ‘Deze bewegende lijn brengt continuïteit in de productie en noodzaakt tot het oplossen van eventuele problemen bij de assemblage. Als er ondanks de vele simulaties en berekeningen toch een manco in het traject zit, moet direct een oplossing worden bedacht. Een gebrek kan alle voordelen van een bewegende assemblagelijn ongedaan maken.’ Maar vooralsnog is Lihart vol vertrouwen. ‘De productiedoelstelling van een toestel per dag is zonder twijfel haalbaar.’
Nieuwsbrief
Vond je dit een interessant artikel, abonneer je dan gratis op onze wekelijkse nieuwsbrief.