
How do you maximise rigidity and minimise weight at the same time? Engineers at Zurich ETH in Switzerland have developed a porous material with a special microstructure, which has a whole range of potential uses.
Modern 3D printing allows structures to be created with dimensions in the microns (thousandth of a millimetre). The Swiss engineers used this method to make a material from plastic that is as light as possible with maximum rigidity, meaning it is highly resistant to deformation when force is applied to it.
The low weight was achieved by building up the material from cube-shaped porous cells, each about 20 microns across. That means material is only present where essential to guarantee strength, and the rest is porous. The design requirement was to achieve maximum strength, equal in all directions, using the minimum amount of material possible.
Cube-shaped cell
The engineers investigated all kinds of shapes to build up the cells. In the end, a structure constructed from tiny panels gave the best results.
The cube cell is made up of three substructures of panels that connect different parts of the cube:
- the centres of the cube planes
- ribs on opposite sides
- the middle of the ribs
Combining these three substructures gave the ideal rigidity, approaching the theoretical maximum. The strength decreases proportionally as the panels become thinner and less resistant to deformation.
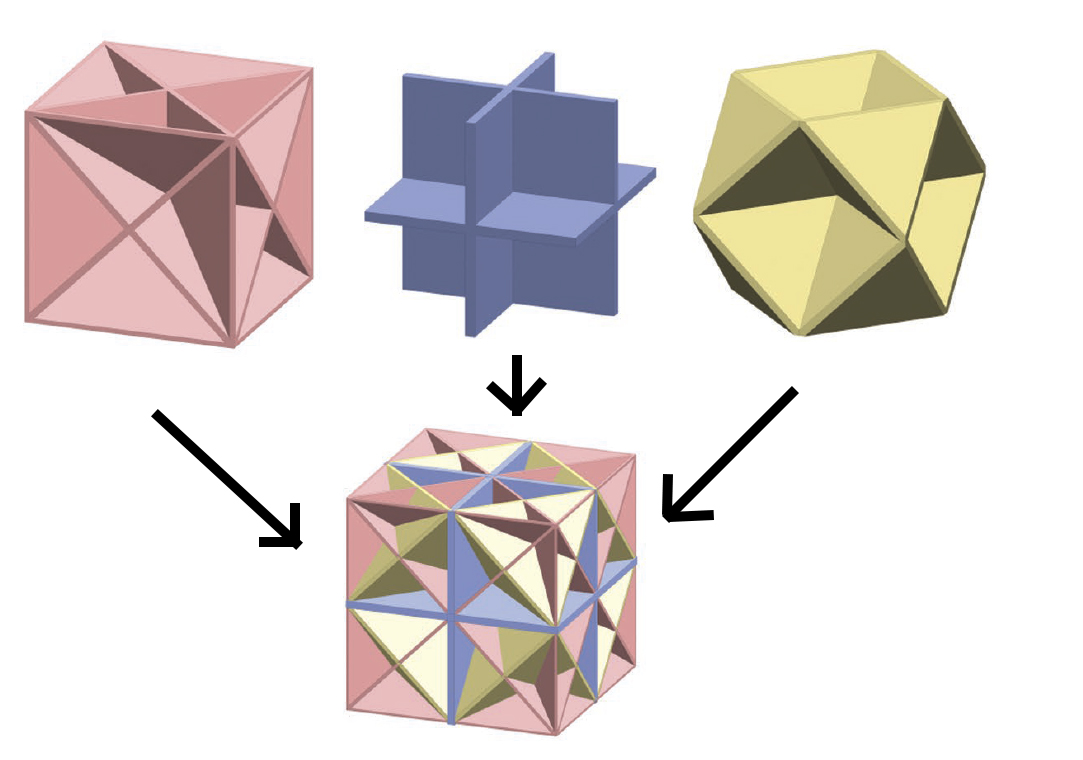
Truss not strong enoug
The result is remarkable, because usually truss are selected to construct such a cube structure, which are then connected to each other with other oblique ones. That works reasonably well for a single cell, but it turns out that if a larger structure is created by stacking a lot of these cells on top of each other, the resulting combination is not particularly strong. In fact, the strength is often just a third of the theoretical maximum.
If the larger structure is constructed from the cells with panels, the rigidity remains high, and is more than three times better than the version with truss. The explanation for this is relatively simple: the panels can absorb forces in two directions, the truss only in one.
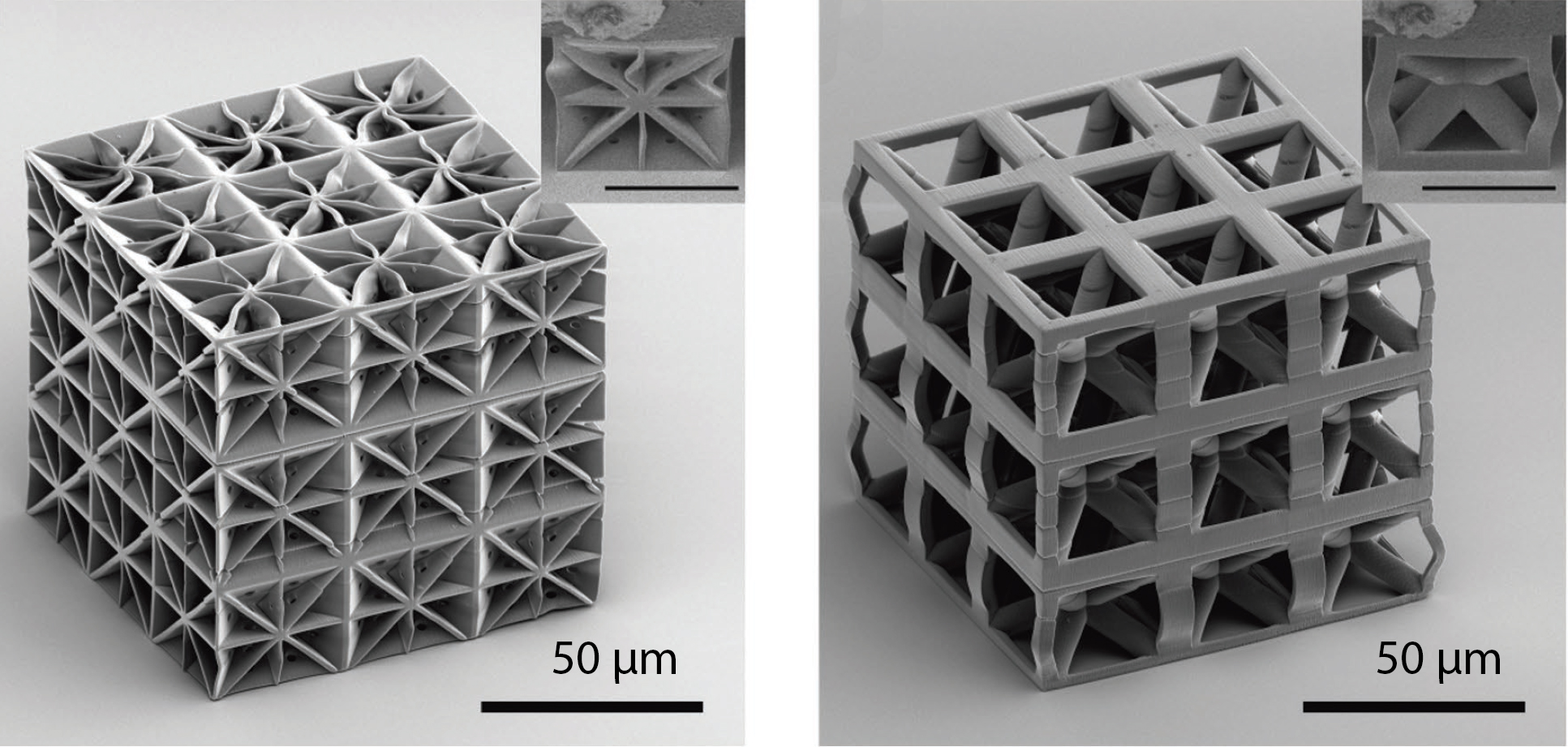
Not as strong as solid material
Making the material porous does make it weaker than solid material. When asked, Thomas Tancogne-Dejean from ETH said that a cell that is 80% porous has one eighth of the strength of a solid cell, but on the other hand it is much lighter.
The engineers envisage numerous applications for the material, for example self-supporting insulation, lightweight structures such as car parts, and medical implants.
If you found this article interesting, subscribe for free to our weekly newsletter!
Nieuwsbrief
Vond je dit een interessant artikel, abonneer je dan gratis op onze wekelijkse nieuwsbrief.