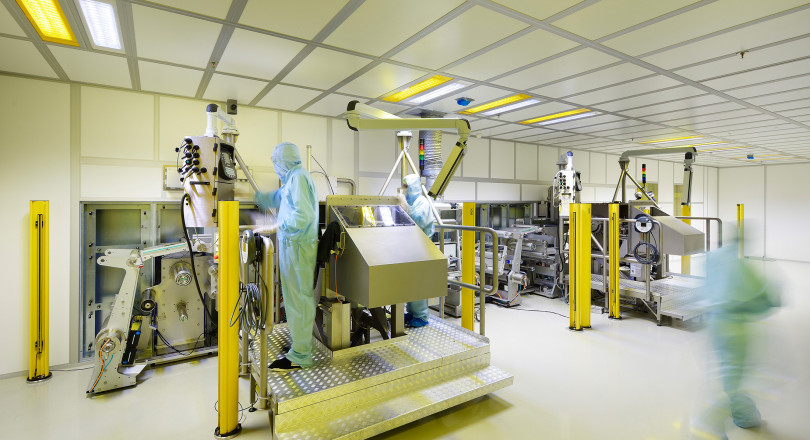
Solliance heeft een nieuwe coatinglijn in gebruik genomen die elke minuut 30 m flexibele zonnecel of organische leds kan printen op folie. ‘Wat chipmachinemaker ASML presteert, willen we nu ook kunnen op het gebied van zonnecellen en organische leds.’
Met de coatinglijn zet Solliance een nieuwe stap in de ontwikkeling van machines die in staat zijn organische zonnecellen en organische leds op folie te produceren en die vervolgens op rol af te leveren. De verwachting is dat de printtechniek de productiekosten van de organische elektronica flink omlaag brengt.
Binnen Solliance is een programma opgezet om zo’n coatingmachine te ontwikkelen. ‘We zijn in Nederland goed in het ontwikkelen van dit soort complexe apparaten’, zegt prof.dr. Pim Groen, programmamanager van het Holst Centre, een van de participanten in Solliance. Daarin nemen verder deel energieonderzoekscentrum ECN, onderzoeksinstituut TNO, het Belgische micro-elektronicacentrum imec, de tu’s van Eindhoven en Delft, en het Duitse Forschungszentrum Jülich. De machine werd medio december 2015 in gebruik genomen, lees hier het persbericht.
Opeenstapeling
In eerste instantie lijkt de opgave eenvoudig. Een organische zonnecel bestaat uit een opeenstapeling van verschillende laagjes: een lichtdoorlatende anode, een actieve laag en een kathode. Om de lichtgevoelige laag af te schermen wordt dit geheel nog eens ingepakt in twee zogeheten barrièrelagen, en dat alles zit op een polymere onderlaag. De organische lagen worden aangebracht als suspensie en per laag in een oven gedroogd.
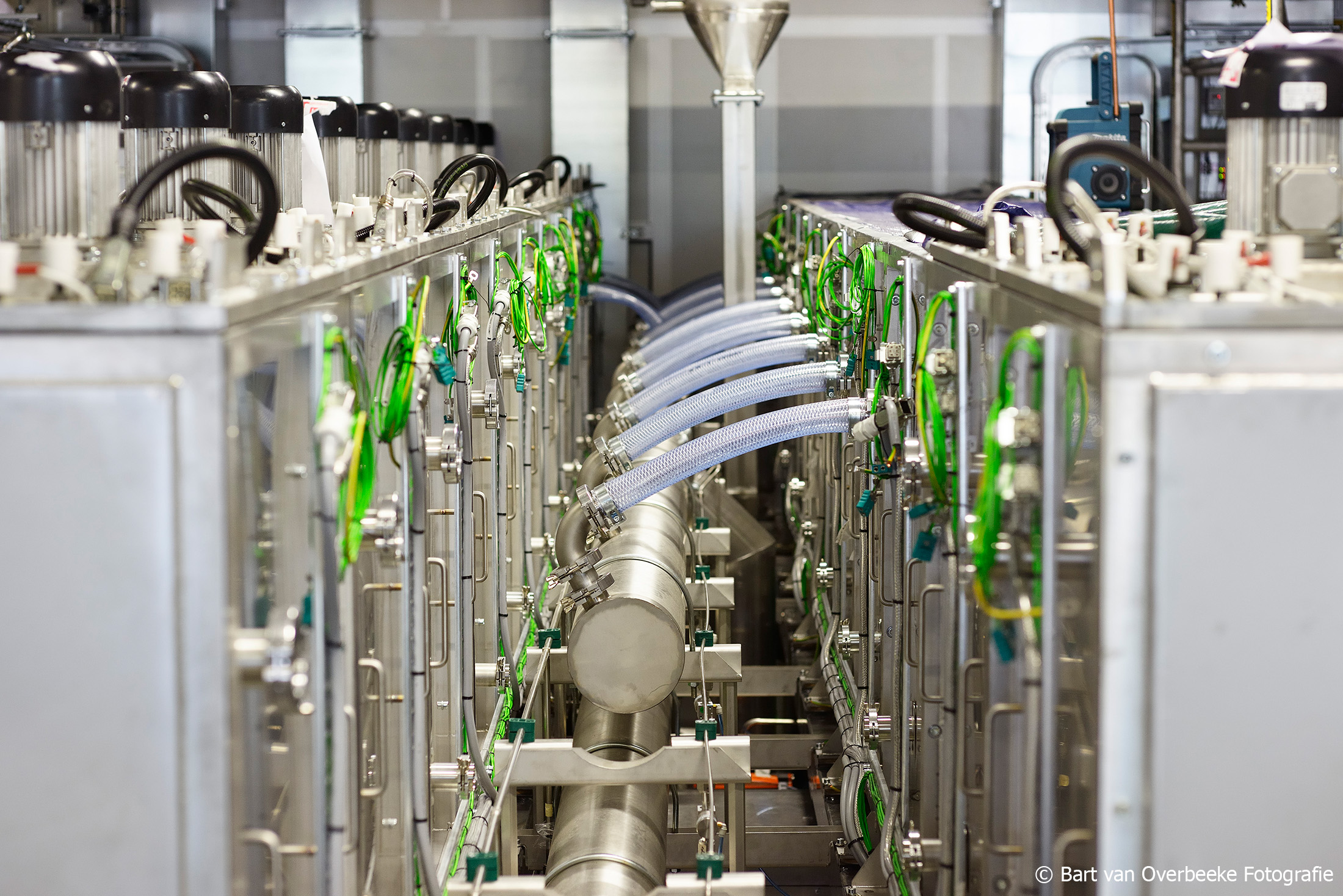
Maar de opgave is immens: bij het produceren van homogene laagjes van zo’n 50 nm dik, zes verschillende precies bovenop elkaar, mag de afwijking over een lengte van de coatinglijn, zo’n 40 m, niet meer zijn dan een tiende millimeter. En die zonnecel of led moet ook nog eens in partjes worden geprint, zodat die uit de folie zijn te snijden.
Afblijven
De nieuwe lijn heeft een aantal specialiteiten. Een ervan is dat de kant van de folie waarop de gevoelige lagen zitten, tijdens het productieproces nergens wordt aangeraakt. Groen: ‘Uniformiteit is cruciaal, want bij een organische led zie je verschillen direct als donkere of lichte vlekken. Zou je met een rol de gevoelige laag raken, dan heb je geen controle meer over de uiteindelijke laagdikte.’ Het betekent dat er een complex mechanisme is gebouwd om de folie van een rol af te wikkelen en vervolgens 40 m verderop, voorzien van zonnecel of led, weer op te rollen. ‘Slip, scheeftrekken, ongelijkmatige spanning, dat willen we allemaal niet.’
Statische elektriciteit
Aparte aandacht vraagt statische elektriciteit. ‘Onder wat voor condities je ook werkt, er zijn altijd wel deeltjes die je niet wilt hebben, maar onze folie wel aantrekt. Dus we doen veel aan antistatica om de ladingopbouw weg te nemen’, vertelt Groen. Het drogen van de nat aangebrachte organische laag gebeurt in speciale ovens. ‘De droogcondities zijn heel strikt, alleen dan lukt het om de suspensie van 0,5 μm dikte te drogen tot een uniforme laag van enige tientallen nanometers.’ Het betekent dat overal op de lijn en in de ovens sensoren het proces in de gaten houden en zo nodig kunnen bijsturen. ‘We meten de laagdikte met optische technieken.’
Smalle sleuf
De gevoelige lagen worden aangebracht via het zogeheten slot-die coaten: onder druk komt suspensie via een smalle sleuf op de folie die vlak daarvoor vacuüm is afgezogen. ‘Die techniek wordt ook elders toegepast.’ Maar Groen wil zonnecellen in partjes kunnen printen. ‘Je moet ze op een bepaalde afmeting kunnen lossnijden.’ Het stoppen van toevoer van de vloeistof of afsluiten met een ventiel is geen optie, omdat het onregelmatige randen geeft. Uiteindelijk is ervoor gekozen de printsleuf van de folie weg te trekken. ‘Daarmee krijgen we wel een mooie rand.’ Punt is alleen dat de printsleuf met al zijn onderdelen ruim 40 kg weegt. ‘We gebruiken een contragewicht. We hebben voor de mechaniek dankbaar gebruik gemaakt van de expertise die TNO op dit gebied heeft.’
De meeste onderdelen van de coatinglijn zijn van Nederlands fabricaat. VDL bouwde samen met Solliance de coatinglijn, de ovens zijn geleverd door Smit Thermal Solutions.
Nieuwsbrief
Vond je dit een interessant artikel, abonneer je dan gratis op onze wekelijkse nieuwsbrief.